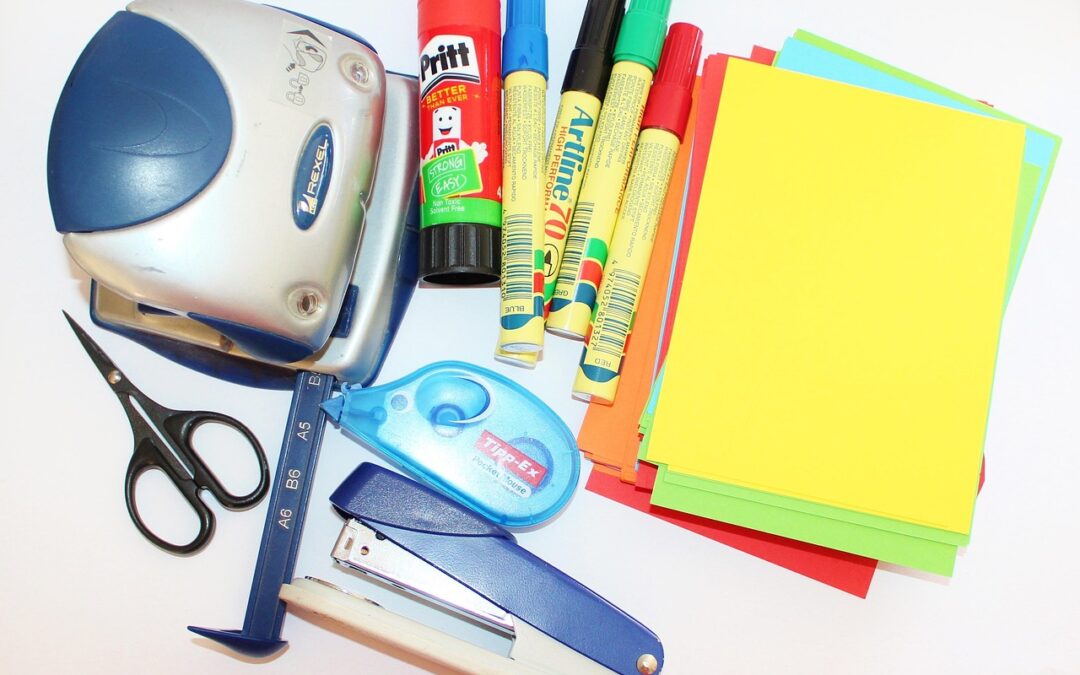
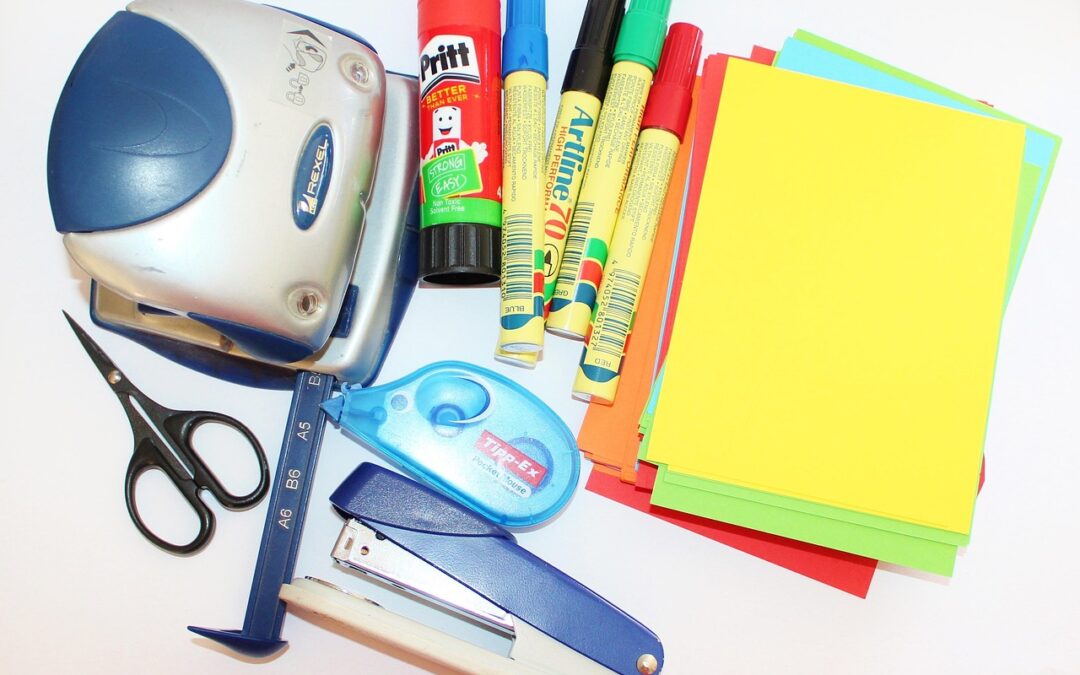
Search
Columbus
45°F
+41
+41
+41
+41
+41
+41
+41
+41
+41
+44
+46
+50
+53
+55
+57
+59
+60
+60
+58
+55
+50
+45
+42
+40
Thu
60°F
40°F
+39
+38
+38
+38
+38
+38
+37
+37
+37
+39
+40
+41
+43
+44
+45
+46
+47
+47
+46
+45
+44
+42
+40
+38
Fri
47°F
37°F
+37
+36
+34
+33
+33
+32
+32
+32
+34
+37
+40
+44
+45
+47
+48
+48
+49
+49
+49
+48
+47
+46
+45
+43
Sat
49°F
32°F
+40
+38
+37
+37
+36
+36
+36
+35
+35
+38
+41
+45
+48
+51
+54
+54
+54
+54
+53
+53
+53
+52
+51
+50
Sun
54°F
35°F
+49
+48
+47
+47
+47
+47
+47
+47
+47
+50
+53
+56
+58
+61
+64
+63
+61
+60
+58
+57
+55
+54
+53
+52
Mon
64°F
47°F
+50
+49
+48
+47
+47
+46
+46
+45
+45
+46
+46
+47
+48
+49
+50
+49
+47
+46
+45
+44
+43
+42
+41
+40
Tue
50°F
40°F
+39
+39
+38
+37
+36
+35
+35
+34
+33
+35
+38
+40
+42
+45
+47
+47
+47
+46
+46
+46
+46
+44
+43
+41
Wed
47°F
33°F
+40
+38
+37
+36
+36
+35
+34
+34
+33
+37
+40
+44
+47
+51
+54
+54
+53
+53
+53
+52
+52
+51
+50
+49
+49
+48
+47
+47
+47
+47
+47
+47
+47
+48
+49
+50
+51
+52
+53
+52
+51
+49
+47
+46
+45
+44
+42
+41
+40
+39
+38
+38
+38
+39
+39
+39
+39
+42
+44
+46
+48
+51
+53
+53
+53
+53
+53
+53
+46
+45
+44
+43
Weather Data Source: Wetter vorhersage 30 tage
You may also be interested in…
- General Contractor In McKees Rocks PA Landscaping Services In McKees…
- Roofing Contractor In Mount Clemens MI Roof Repair Services In…
- Business Development Consulting: The Ultimate Guide TL;DR Unlock the potential…
- Appliance Removal Services Near Me: Appliance Removal Services: Unburden Your…
- Find Local Services » Discover The Ultimate Guide To Finding…
Check out these locations…
More locations to choose from…
Checkout these too…
- General Contractor In McKees Rocks PA Landscaping Services In McKees…
- Roofing Contractor In Mount Clemens MI Roof Repair Services In…
- Business Development Consulting: The Ultimate Guide TL;DR Unlock the potential…
- Appliance Removal Services Near Me: Appliance Removal Services: Unburden Your…
- Find Local Services » Discover The Ultimate Guide To Finding…
From the Blog
- Accounting & Bookkeeping
- Advertising & Marketing
- Airport Hotels
- Automotive
- Bed & Breakfasts
- Books & Stationery
- Boutique Hotels
- Business & Professional Services
- Carpet Cleaning
- Churches Temples and Religious Sites
- Clothing & Apparel
- Conference Hotels
- Cultural Attractions
- Designer Hotels
- Diesel Repair & Service
- Dining Experience
- Discover More
- Eco-Friendly Hotels
- Education & Training
- Electrical
- Electronics & Gadgets
- Events & Festivals
- Everything Else
- Extended Stay
- Family & Kids
- Family-Friendly Hotels
- Features & Amenities
- Flooring
- Food & Beverage
- Food & Cuisine
- Food & Drink
- Garden Weed Control
- Handyman
- Health & Beauty
- Heating & Air Conditioning
- Historical Sites
- Home & Garden
- Hostels
- Hotels with Casinos
- Hotels with Spas
- In the News
- Inns
- Janitorial
- Jewelry & Watches
- Landscaping
- Location
- Luxury Hotels
- Malls
- Nightlife
- Noxious Weed Control
- Occasions
- Office Supplies
- Online Stores
- Outdoor Activities
- Outlets
- Painting
- Parks & Nature
- Personal Care
- Pest Control
- Pet Supplies
- Pet-Friendly Hotels
- Photography Spots
- Plant Fertilization
- Plant Fertilzation
- Plumbing
- Price Range
- Recreation & Outdoors
- Recreational Activities
- Remodeling
- Resorts
- Roofing
- Second-hand Stores
- Self Storage
- Shopping
- Shopping Centers
- Snow Removal
- Specialty
- Specialty Stores
- Spiders
- Sports & Outdoors
- Themed Hotels
- Tile Marble & Stone
- Toys & Hobbies
- Unique Experiences
- Unique Stays
- Vacation Rentals
- Vending Equipment & Spply
- Website Design Hosting & SEO
- Wellness & Relaxation
- Wheelchair Accessible
- WordPress Hosting
- WordPress Maintenance